자주 질문을했습니다.
자주 질문을했습니다.
We’ve put together some commonly asked questions to give you more information about 이중 롤러 압출 과립 화기 we offer.
답을 찾을 수 없다는 질문이 있다면, please use the contact page!
인산염 이집트 공장의 비료 과립 장비
어떻게 할 수 있습니다 A 건조 압출 과립 화기는 유기 비료 과립을 감소시킵니다 생산 비용?
irstly, 사용 a double roller press granulator 유기농 비료 과립을 생산하는 가장 경제적 인 방법 중 하나입니다.. 이 펠트 타이저는 건조 과립을 사용합니다. 또한, 그것은 물이나 바인더가 필요없이 기계적 압출을 통해 유기 비료 펠릿을 형성합니다.. 따라서, 이 기계는 장비 투자를 크게 줄입니다, 건조기와 같은, 쿨러, 먼지 제거 시스템.
아름답게 성취하는 방법 둥근 모습 유기 비료 과립?
티건식 입금기에 의해 생성 된 유기 비료 입자의 형태는 완벽한 둥근을 달성하지 못할 수 있습니다.. 세분화 된 유기농 비료를 더 매력적으로 보이게합니다, 연마기를 구입할 수 있습니다. 초기 비료 과립이 어떤 불규칙한 형태에도, 기계는 한 과정에서 매끄럽고 구형 공으로 굴릴 수 있습니다., 높은 공 형성 속도와 반품 재료가없는. 그 다음에, 이 프로세스는 과립 품질을 향상시키고 시장 매력을 높입니다..
저예산 유기농 비료 생산 계획에 스크리닝 머신을 사용하는 이유?
비앞에, 균일 한 유기 비료 과립 크기를 보장하기 위해 로터리 스크리닝 머신을 구입하도록 선택합니다.. 일관된 과립 크기는 유기농 비료 제품의 품질을 향상시킬 수 있기 때문에. 강력한 분류 기능은 대형 크기 또는 소형 과립을 제거합니다, 고품질 비료의 직접 포장을 허용합니다.
다른 원료가 롤러에 어떤 영향을 미칩니 까 주사위 수명?
드라이 롤러 프레스 삭제기의 롤러 쉘의 수명에 영향을 미치는 몇 가지 요인이 있습니다., 동안 원자재의 유형을 포함합니다 extrusion granulation process. 게다가, 롤러 몰드는 필수 구성 요소입니다, directly impacting the efficiency and longevity of the entire extruder granulation equipment. Here is an analysis of common raw materials and their impact on roller die longevity.

≤1500 톤의 일반적인 NPK 분말 건조 과립
사실은, 일반적인 NPK 재료 또는 특정 미네랄 파우더를 사용하는 경우, 롤러에 더 많은 마모가 발생하지 않습니다.. 일반적으로, 표준 조건에서, 이중 롤러 비료 구조기는 최대까지 지속될 수 있습니다 1500 톤 ~의 NPK 과립 비료 생산. For example, 요소, 황산 암모늄, 염화 암모늄, 탄산 칼슘, limestone, zeolite, 벤토나이트 및 기타 유사한 가루 또는 덩어리. 게다가, NPK 비료 분말을 과립 화를 위해 직접 압출 할 때, 다른 보조 자료를 추가 할 필요가 없습니다. 하지만, 미세한 미네랄 가루에서 화합물 비료 과립을 만드는 경우, 두 롤러만으로는 압출 압력이 충분하지 않습니다.. 또한, 당신은 추가 할 수 있습니다 20% 더 나은 과립 효과를 위해 적절하게 물.
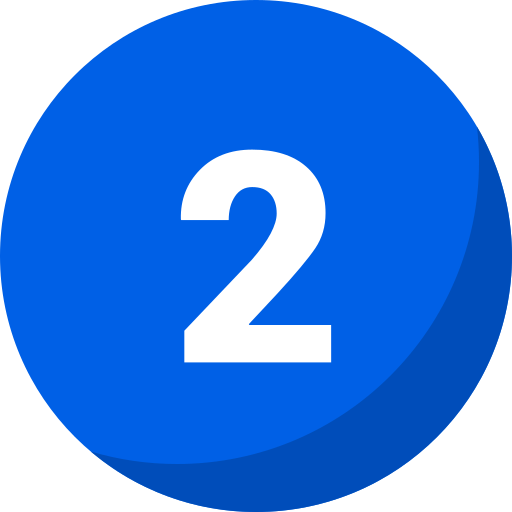
≤800 톤의 부식성 재료 롤러 프레스 과립
In general, 일부 화합물 비료 재료는 약간 산성입니다. 롤러 가이 재료를 누를 때, 온도가 상승합니다. 그러므로, 특정 물리적 및 화학 반응을 통해, 이 원료는 장기간 롤 코팅 및 볼 소켓 모양을 부식시킬 수 있습니다.. 솔직히, 이 압출기 펠트 화기는 대략 생성 할 수 있습니다 800 tons of 부식성 물질의 비료 과립. 예를 들어, 당신은 사용할 수 있습니다 염화 암모늄, 질산 칼륨, 클로라이드 칼슘, 질산 칼슘, manganous sulfate, 모노 암모늄 포스페이트, 등. 비료 펠렛을 만들기 위해. 더 이상, 정기적 인 청소 및 유지 보수는 롤 다이의 서비스 수명을 연장 할 수 있습니다..
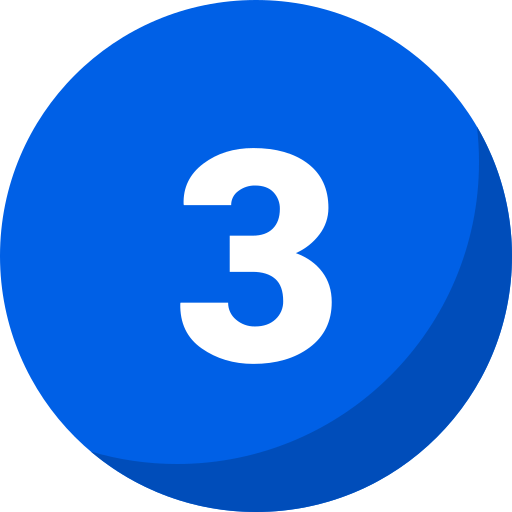
≤500 톤의 유기농 비료 과립 소형 생산
물론, 유기 비료 과립 화자에는 닭 분뇨가 포함됩니다, 돼지 분뇨, kitchen waste, 톱밥, 콩 드레그, 바이오 가스 잔류 물, 버섯 잔류 물 등. At the beginning, 발효 및 분해를 위해 퇴비 기계로 이러한 재료를 처리해야합니다.. 유기 비료 퇴비 후, 이 자료에는 포함됩니다 30-35% 수분 함량. 과립 화 전에 며칠 동안 물을 줄이기에 나이가 더 낫습니다.. 유기농 퇴비는 수분이 높고 강한 끈적 끈적한 것이기 때문입니다, 롤 금형을 막고 손상시키는 것은 쉽습니다.. As a result, 이중 롤러 압축 펠레타이저는 최대 수명의 처리가 있습니다. 500 톤 유기 폐기물의.
비료 롤러 입상기 기계의 서비스 수명을 연장하는 방법?
적절한 유지 보수 롤러 과립 기계의 서비스 수명을 크게 확장 할 수 있습니다.. 첫 번째, 정기적 인 청소가 중요합니다. 잔류 물을 제거합니다, 특히 부식성 재료를 처리 할 때. 둘째로, proper lubrication reduces friction and prevents the machine parts from wearing out prematurely. 게다가, 연산자는 과립기에 과부하를 피해야합니다, 과도한 하중이 마모를 가속화 할 수 있습니다. 마지막으로, 롤러 스킨을 자주 검사해야합니다.. 그 다음에, 추가 손상을 방지하기 위해 마모 된 부품을 즉시 교체 할 수 있습니다..
Top 2 Metal Materials of Double Roller Sheets For Your Choice
The roller skin is a vital component of a double roller granulator, playing a pivotal role in the organic fertilizer or compound fertilizer granulating process. As you operate this machinery, good roller skin benefits the granule production efficiency and longevity of this equipment, and the quality of the final pellets. 따라서, choosing the appropriare material to make the roller sheets is our duty for customers’ actual fertilizer granulation and cost-effectiveness.

Traditional Roller Skin Material of 20CrMoTi For Common Usage
솔직히 말하자면, most of the roller press granulators on the market use 20CrMoTi as roller sheets. 물론, it is a GB standard structural alloy steel with high performance. 또한, it’s a carburizing steel, which is usually a low-carbon steel with a carbon content of 0.17%-0.24%. The composition of 20CrMoTi includes chromium, molybdenum, and titanium. After quenching, it contributes to the roller sheets’ hardness and wear resistance, meeting intense requirements of the dry granulation process. 또한, 20crmnti steel has good weldability, small deformation, and good fatigue resistance. So we can easily carve all kinds of shapes for ball socket on the roller skins according to client’s needs. Its good hardness and toughness and can maintain roll dies non-deformation under high pressure over an extended period. 따라서, we ensure that our extrusion granulators meet the rigorous demands of modern industrial applications by using 20GrMoTi.
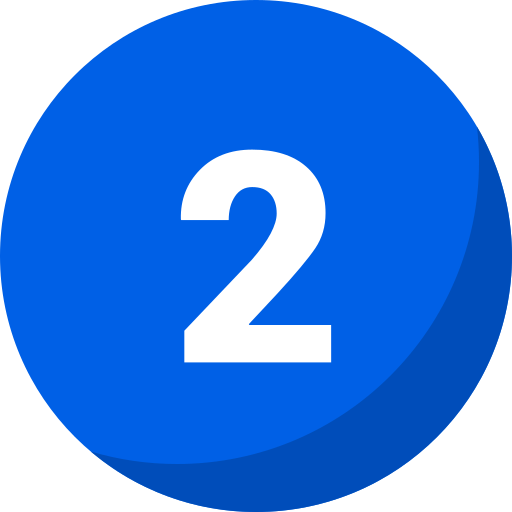
New Roller Skin Material of 4Cr13 For High-quality Granulation
In recently years, our company applies new material to manufacture double roller compact granulator, 4CR13. Compared to the traditional alloy steel, 4CR13 is martensitic stainless steel. 더 이상, the special composition of 4CR13 steel, including carbon, silicon and manganese content, contributes to its outstanding properties. Our factory quenches the roller dies made of 4CR13 steel to get a harder surface. Compared to other steels, it is worth mentioning its excellent resistance to corrosion and polishing performance. 그래서, the polishing property of this material also contribute to the beautiful and smooth surface of the roll pelletizer we produce. 그러므로, this customization roll die of roller pressing granulator is ideal for handling corrosive raw materials like animal manure, 등. It prevents raw materials from sticking to the ball socket and corroding the equipment. Above all, using 4CR13 steel as the roll dies’ material extends granulator’s service life in industrial granulation process.
What Is The Cost Difference Between Roller Sheet Materials 20crmnti And 4Cr13?
전문 비료 장비 제조업체로서, 유 룬신 provides detailed information on the cost difference between roller sheet materials 20CrMnTi and 4Cr13. The market price for 20CrMnTi is approximately $1.2–$1.5 per kilogram, while 4Cr13 ranges from $2.0–$2.5 per kilogram. 일반적으로, a roller granulator with a capacity of 1 ton per hour, is priced around $4000. 게다가, the roller molds made from 20CrMnTi would cost about $240-$300. 대조적으로, molds made from 4Cr13 would cost approximately $480-$600. 따라서, customers can evaluate the material choice based on budget and performance needs.
The double roller extrusion granulator, also known as a dry granulation press or roller compactor, is a pivotal piece of equipment in the granulation process, which transforms fine powders into densified and compacted granules. The machine’s structural material is of paramount importance, as it needs to endure continuous operational stress and strain. For this reason, the main frame and components of the extrusion granulator are constructed from boiler steel, specifically the Q235 grade.
This material is renowned for its impressive strength and resilience, making it an excellent choice for heavy-duty machinery. Q235 boiler steel is characterized by its high tensile strength and yield point, ensuring that the machinery can withstand the substantial pressure exerted during the compaction process. 게다가, its resistance to deformation and cracking under stress guarantees a long service life for the granulator, ultimately leading to reduced maintenance requirements and operational downtime.
따라서, the utilization of Q235 boiler steel in the construction of the extrusion granulator not only ensures the robustness and longevity of the machinery but also underpinning the reliability and consistency of the granulation process.
The double roller press granulator is a versatile tool for dry powder granulation, comfortably processing a wide array of chemical and organic materials.
1. Raw Materials in NPK Fertilizer Production
A double roller extrusion granulator, utilizing roller compaction technology, efficiently processes an extensive range of materials in fertilizer production. These materials include compound fertilizers such as ammonium sulfate and ammonium nitrate, phosphate fertilizers like monoammonium phosphate (MAP) and diammonium phosphate (튐), potash, and so on.
2. Handling Organic Materials for Fertilizer Production
Besides chemical fertilizers, the granulator excels in processing organic materials pivotal for organic fertilizer production. Examples include animal manure, compost, and sludge, which are crucial components of organic fertilizers. Its efficiency, 적응성, and reliability make it a preferred choice for organic fertilizer manufacturers seeking high-quality granulation proposals.
3. Other Applications in Dry Powder Granulation
Beyond fertilizer production, the double roller extrusion granulator finds application in various industries requiring dry powder granulation. 또한, it’s utilized in the chemical industry for the compaction of powdered materials into solid forms, facilitating handling and storage. 게다가, the granulator efficiently handles mineral powders, contributing to applications such as metallurgy and mining. 예를 들어, it processes mineral powders into dense granules for use in metallurgical processes or as additives in various industrial applications.
Conclusion
With its capability to process a diverse array of materials, ranging from chemical fertilizers and organic substances to mineral powders, the double roller extrusion granulator emerges as a versatile and indispensable tool in dry powder granulation across multiple industries. 그 동안에, you should know the key for successful granulation is to understand the material’s characteristics, including particle size, 수분 함량, and cohesiveness. Slightly adjusting the roller gap and pressure settings allows for the production of granules with the desired density and size.
At the beginning, you must understand that maintaining a double roller extrusion granulator is essential for it to function optimally. Regular maintenance not only extends the machine’s lifespan but also ensures you get the best performance. As an operator, remember that your attention to maintenance details will prevent unexpected breakdowns and costly repairs.
1. Daily Maintenance Routine
Every day, you should start by cleaning the machine to remove any residual material that could harden and cause blockages. 뿐만 아니라, you should check the machine’s parts, such as bolts and bearings, to ensure they are tight and in good condition. 또한, lubricate the moving parts to reduce wear and tear. Importantly, you should inspect the rollers and die for any signs of damage or wear. If you notice any issues, address them immediately to prevent further complications.
2. Weekly Maintenance Tasks
In addition to daily maintenance, there are tasks you should perform weekly. These include a thorough inspection of the electrical system to ensure there are no loose connections or damaged wires. 게다가, you need to check the pressure of the rollers and adjust if necessary to ensure uniform granules. 뿐만 아니라, you should find professional engineers to assess the machine’s overall performance and efficiency. If you detect any irregularities, it’s crucial to troubleshoot them promptly.
3. Monthly Maintenance Checks
On a monthly basis, you should conduct more in-depth maintenance. This involves checking the gearbox oil level and quality, and replacing it if needed. 또한, tou can examine the belts for any signs of wear or slackness and adjust or replace them accordingly. 또한, you should test the machine’s safety features to ensure they are functioning correctly. Remember, safety checks are not just about compliance, but they also protect you and your workers from potential hazards.
4. Long-term Maintenance Schedule
Finally, for long-term maintenance, you should schedule downtime for the machine at least once a year. During this period, you can perform comprehensive maintenance tasks such as replacing worn-out parts, updating any outdated components, and thoroughly cleaning and inspecting every part of the machine. 또한, you can contact us for replacement of wearing parts.
전반적인, maintaining your double roller extrusion granulator requires diligence and consistency. By following the daily, weekly, monthly, and long-term maintenance schedules, you ensure the machine operates at peak performance for more than 10 years. If you have any further questions or concerns, don’t hesitate to consult the manufacturer’s manual we provide or contact our professional technician for assistance.
1. What Is The Basic Principle?
The fertilizer roller granulator machine operates on the principle of compaction and granulation. 게다가, through the application of pressure, raw materials are compacted into dense masses, which are then broken down into uniform granules. 게다가, this process occurs without the use of additional moisture, making it ideal for producing dry fertilizer granules.
2. How Does The Extrusion Process Occur?
During operation, the granulator press roller machine utilizes counter-rotating rollers to exert pressure on the raw materials. 그 다음에, this pressure forces the materials to pass through the narrow gap between the rollers, resulting in compaction. As the compacted material exits the rollers, it undergoes further processing to form granules of the desired size and shape.
3. What Are The Key Components?
Key components of the roller granulating machine include the extruder, which places the counter-rotating rollers, and the feeding system, responsible for delivering raw materials to the extrusion zone. 또한, the granulation chamber and discharge system play crucial roles in shaping and collecting the formed granules.
4. What Are the Advantages of Dry Granulation?
Dry granulation offers several advantages over traditional wet granulation methods. By eliminating the need for additional moisture, it reduces production costs and energy consumption. 게다가, dry granulation minimizes the risk of material degradation and contamination, resulting in higher-quality granules.
5. What Are Applications of Press Roller Machine?
Dry roller press granulators find application in various industries, including fertilizer production, chemical manufacturing, mining processing, and food processing. 게다가, they are particularly suitable for producing granular products with specific size and density requirements, making them indispensable in modern manufacturing processes.
1. What Makes the Double Roller Extrusion Granulator Essential?
첫 번째, double roller extrusion granulator serves as key equipment in compound fertilizer granulation. With advanced technology, compact structure, and low energy consumption, this device operates on the extrusion principle to swiftly form fertilizer granules ranging from 3 to 10mm in diameter.
2. Where Does the Roller Press Granulator Find Application?
둘째로, this dry granulator is indispensable in the production of special compound fertilizers of varying concentrations for diverse crops. Whether high, medium, or low concentration compounds, the roller press granulator can achieve all the results. 그 동안에, it doesn’t need drying and cooling process, which makes it suit various materials’ granulation.
3. What Are Commercial Proposals of Double Roller Press Granulator?
From an investment and economic perspective, the pellet extruder machine proves highly advantageous across several industries. 우선, it can be applictions in fertilizer processing, feed production, and chemical industry granulation. 뿐만 아니라, it finds applications in powder material production and processing, with notable relevance in sectors such as rare earth, 야금, coal, biological preparations, and environmental protection engineering for sludge treatment.
4. How to Optimize Granular Fertilizer Production Efficiency?
Fourthly, to cater to customer demands effectively, our factory offers the flexibility to design and manufacture accompanying equipment. From mixers and crushers to bucket elevators and conveyors, you have many options for your fertilizer production efficiency enhancement. 또한, automatic batching machines and rotary screening machines enhance the efficiency of compound fertilizer production lines, facilitating continuous and mechanized operations.
5. What Materials Can Be Used in the Roller Extrusion Granulator?
The double roller type fertilizers granule machine accommodates a wide array of materials for extrusion granulation. These include ammonium nitrate, 요소, 염화 암모늄, 질산 칼슘, potassium chloride, 황산 칼륨, and more. With its versatility and efficiency, this equipment seamlessly integrates into various production processes, ensuring consistent and high-quality granule formation.
사실은, water content of raw materials is a key parameter for the double roller granulator that significantly impacts the overall efficiency and quality of the granulation process. When you use our double roller type fertilizers granule machine, we recommend to maintain the materials’ moisture content of 5%-10% to achieve optimal granulating results.
Why to Control 5%-10% Material Water Content for Dry Granulation Roller Compaction?
Why is controlling the moisture important when using YSX double roller granulator? 따라서, several reasons account for the significance of this specific range of water content.
- 첫 번째, you can ensure the proper granular forming during the press granulation process by maintaining the right moisture level in the raw materials.
- If there’s too much water (more than 10%), you may end up with wet finished granules that stick together, forming lumps. 그 다음에, it causes difficult separation and impairs the uniformity of your final products.
- 거꾸로, raw materials without enough moisture (less than 5%) might not support conditions of particle adhesion, leading to granules that are too dry and break down easily.
As a result, only the moisture content within the recommended range, the particles can adhere together smoothly, resulting in well-formed and sturdy granules. This ensures that the granules are resistant to breakage and can withstand handling and transportation without losing their integrity.
To conclude, finding the right moisture balance is paramount for producing high-quality granules in a double roller granulator. If you aren’t sure about the moisture content of your raw materials, feel free to send them to us. We would be more than happy to carry out an analysis for you and guide you towards the most effective process possible.
Customers often ask about the longevity and durability of our granulation machinery. 게다가, two common question are, “What is the wearing part?” or “How long does it take to replace the mold?”
What is the wearing part?
첫 번째, let’s understand what worn parts refer to. In Shunxin’s roller granulator, the worn parts are the roller sheets. 우선, two rollers are made of special alloy materials to endure high pressure and wear during the dry granulation process. 다른 일을 위해, you don’t need to worry about the replacement of two rollers. If you normally use and maintain double rollers pressing granulator according to the operating instructions, the service life of 2 rollers can reach at least 6 months. 하지만, when you find that the roller is worn or the granulation quality is getting worse, you should consider replacing it with a fresh roller.
How long does it take to replace the mold?
둘째로, you should know the time for replacing the mold. 전반적인, in most cases, you may need to replace the rollers within 6 months 에게 1 year. 뿐만 아니라, many elements will impact the particular time, including frequency of usage, raw materials’ kind and quality, and so on. To guarantee the performance of the rollers and the efficient operation of this granulator, we recommend that you regularly inspect and perform necessary maintenance. If you see that the roller is worn out or that the granulation effect is poor, it is time to replace it.
Conclusion
Our roller pressing granulator is a reliable equipment. By regularly replacing two rollers and maintaining these molds, you can keep the machine running smoothly and achieve high-quality granulation effects. 대체로, we are committed to providing cost-effective organic fertilizer production proposals. 따라서, choosing Shunxin’s roller granulating machine would be a wise choice. If you have any further questions or requests, we are always willing to provide assistance and support.
Maintaining your double roller extrusion granulator is essential to ensure its longevity and optimal performance. Regular upkeep not only prevents unexpected breakdowns but also guarantees that your fertilizer production runs smoothly and efficiently. Here’s a comprehensive guide on how to maintain your granulator:
Step 1: Regular Cleaning and Inspection
첫 번째, to maintain your double roller press granulator effectively, it is crucial to conduct regular cleaning and inspection. At the beginning, you can start by disconnecting the power source and removing any remaining materials. 게다가, you should use a brush or compressed air to clean the rollers and the surrounding areas. 그 동안에, you can inspect the rollers for any signs of wear or damage. By keeping the machine clean and performing regular inspections, you can prevent potential issues and ensure smooth operation.
Step 2: Lubrication of Moving Parts
둘째로, proper lubrication of moving parts is essential for the efficient operation of the roller extrusion granulator. 그래서, you may use the recommended lubricants and follow the our professional equipment manufacturer’s guidelines for lubrication intervals. 또한, you can apply the lubricant to the designated points, including bearings, gears, and other moving components. Importantly, it will reduce friction, minimize wear and tear of well-lubricated parts, and extend the lifespan of the machine. 뿐만 아니라, you can regularly check the lubrication status and replenish as needed to maintain optimal performance.
Step 3: Adjustment of Roller Gap
셋째, the adjustment of the roller gap is a critical maintenance task for a roller compaction granulator. Because, proper roller gap settings ensure the desired granule size and density. 게다가, you should follow our recommendations for adjusting the roller gap based on the type of raw materials being processed. 게다가, you should regularly check and adjust the roller gap as needed to maintain consistent granulation performance. By ensuring the correct roller gap settings, you can produce high-quality granules and prevent issues such as uneven granule size or blockages.
Step 4: Replacement of worn parts
Fourthly, parts of your granulator will inevitably wear out due to regular use. 그래서, you must keep a close eye on components that tend to wear out quickly, such as rollers, bearings, and seals. 게다가, you can inspect these parts frequently for any wear signs, including cracks, dents, or excessive wear. Once you notice that parts are worn, replace them immediately with genuine parts. 또한, you can contact us to have new parts shipped for free shipping during the warranty period. 따라서, timely replacement of worn components helps you avoid operational interruptions, maintain granulation quality, and extend the overall life of your machine.
Step 5: Optimizing Material Handling
Finally, proper material handling is key to the maintenance of a dry extrusion granulator. For example, you need to ensure that the raw materials fed into the machine meet the specified requirements in terms of moisture content, particle size, and composition. 또한, you should also avoid overloading the machine to prevent undue stress and damage. 또한, you can regularly clean the material feeding system to prevent clogs and ensure smooth material flow. By optimizing material handling practices, you can maximize the efficiency and productivity of the granulation process while minimizing wear on the machine.
Conclusion
전반적인, maintaining a double roller extrusion granulator involves a combination of regular cleaning, lubrication, adjustments, part replacements, and material handling optimization. By following these maintenance guidelines diligently, you can ensure the longevity, efficiency, and quality performance of your granulation equipment. Because it not only increases productivity but also minimizes downtime and repair costs in the long run.
Here at Yushunxin, we take pride in the efficiency and performance of our 이중 롤러 압출 과립 화기. 게다가, our engineers design this machine expertly to convert various raw materials into granules, commonly in industries like fertilizer, feed, and chemical. 게다가, one of the standout features of our granulator is that it produces granules with consistent size and hardness.
티ypically, the final granule size you can expect by using our roller press granulator is in the range of 3-10mm. In other words, you can adjust the machine’s parameters to control the sizes, including the pressure and the distance between two rollers. 게다가, you understand that granule size matters when it comes to applications like fertilizer production, as it affects nutrient distribution and absorption in the soil. 그러므로, we ensure our granulator produce a size range optimal for you needs.
In addition to size, the hardness of the granules by dry roller press granulator is usually around 15-20N/mm2. 따라서, this level of hardness ensures the granules are durable and not prone to breaking or crumbling during handling or application. As a result, it depends on the pressure by the two rollers and the composition of the raw materials.
It’s essential to note, however, that granule size and hardness can somewhat vary with different materials and granulator settings. 그러므로, operators need to carefully control these parameters to achieve the desired granule characteristics.