Frequently asked questions.
Frequently asked questions.
We’ve put together some commonly asked questions to give you more information about double roller extrusion granulator we offer.
If you have a question that you can’t find the answer, please use the contact page!
How Do Different Raw Materials Affect Roller Die Lifespan?
There are several factors influencing the lifespan of roller shells of dry roller press granulator, including the type of raw materials during the extrusion granulation process. Moreover, roller molds are essential components, directly impacting the efficiency and longevity of the entire extruder granulation equipment. Here is an analysis of common raw materials and their impact on roller die longevity.

≤1500 Tons of Common NPK Powder Dry Granulation
In fact, if you use common NPK materials or certain mineral powders, it won’t cause more wear and tear on the rollers. Typically, under standard conditions, double roller fertilizer granulator can last up to 1500 tons of NPK granular fertilizer production. For example, urea, ammonium sulfate, ammonium chloride, calcium carbonate, limestone, zeolite, bentonite and other similar powder or lumps. Moreover, when extruding NPK fertilizer powder directly for granulation, you needn’t to add other auxiliary materials. However, if you make compound fertilizer granules from finer mineral powder, the extrusion pressure between the two rollers alone is not enough forming. Also, you can add 20% water appropriately for better granulation effect.
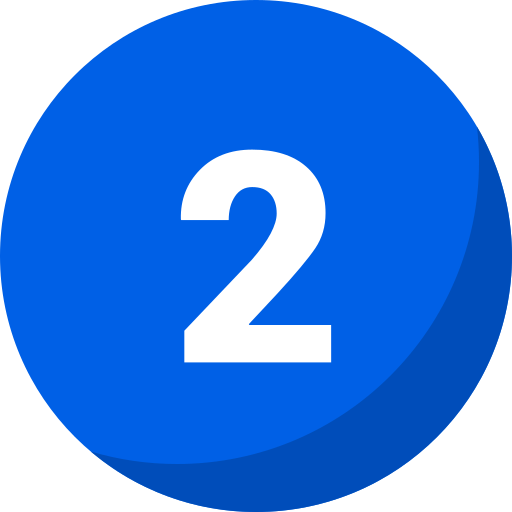
≤800 Tons of Corrosive Materials Roller Press Granulating
In general, some compound fertilizer materials are slightly acidic. When the rollers press these materials, the temperature will rise up. Therefore, through certain physical and chemical reactions, these raw materials can corrode the roll coating and ball socket shape over a long period of time. Honestly, this extruder pelletizer can produce approximately 800 tons of fertilizer granules from corrosive substance. For instance, you can use ammonium chloride, potassium nitrate, calcium chloride, calcium nitrate, manganous sulfate, monoammonium phosphate, etc. to make fertilizer pellets. What’s more, regular cleaning and maintenance can extend the service life of the roll dies.
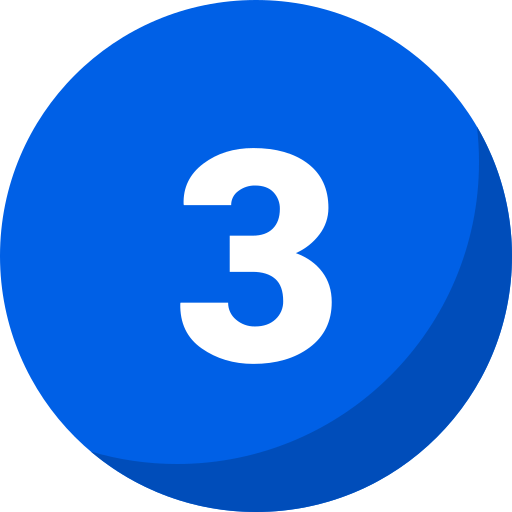
≤500 Tons of Organic Fertilizer Granule Compact Production
Indeed, organic fertilizer granulation raw materials include chicken manure, pig manure, kitchen waste, sawdust, bean dregs, biogas residues, mushroom residues and so on. At the beginning, you should handle these materials by compost machines for fermentation and decomposition. After organic fertilizer composting, these materials contain 30-35% moisture content. And you’d better age to reduce water for a few days before granulation. Because organic compost has high moisture and strong stickiness, it is easy to clog and damage the roll molds. As a result, double roller compaction pelletizer has a maximum lifespan of processing 500 tons of organic waste.
How to Extend The Service Life of Fertilizer Roller Granulator Machine?
Proper maintenance can significantly extend the service life of roller granulating machine. Firstly, regular cleaning is crucial. And you remove residues, especially when processing corrosive materials. Secondly, proper lubrication reduces friction and prevents the machine parts from wearing out prematurely. In addition, operators should avoid overloading the granulator, as excessive load can accelerate wear. Lastly, you should frequently inspect the roller skins for wear and tear. Then, you can replace worn-out parts promptly to prevent further damage.
What is the key part for operational efficiency of a double roller extrusion granulator? Besides, what is the important section of an roller extruder granulator or roller compaction technology. Of course, they are the roller sheets. These sheets are the primary contact points where powders are pressed into uniform granules. Therefore, the material chosen for the roller sheets must exhibit outstanding strength and durability to withstand the pressure and friction of the process.
For this reason, the roller sheets are made from 20GrMoTi, a high-performance alloy that provides exceptional wear resistance and mechanical properties suitable for the intense requirements of the dry granulation process. The composition of 20GrMoTi includes chromium, molybdenum, and titanium, which contribute to the alloy’s hardness and stability, ensuring that the roller sheets maintain their shape and functionality over an extended period, even under continuous operation.
The use of 20GrMoTi in the construction of roller sheets enables the granulation machinery to operate at peak efficiency, producing high-quality granules with consistent size and density. It also reduces the frequency of maintenance and replacement, thereby enhancing the overall productivity of the granulation process.
By incorporating 20GrMoTi into the design of the roller sheets, we ensure that our extrusion granulators are equipped to meet the rigorous demands of modern industrial applications.
The double roller extrusion granulator, also known as a dry granulation press or roller compactor, is a pivotal piece of equipment in the granulation process, which transforms fine powders into densified and compacted granules. The machine’s structural material is of paramount importance, as it needs to endure continuous operational stress and strain. For this reason, the main frame and components of the extrusion granulator are constructed from boiler steel, specifically the Q235 grade.
This material is renowned for its impressive strength and resilience, making it an excellent choice for heavy-duty machinery. Q235 boiler steel is characterized by its high tensile strength and yield point, ensuring that the machinery can withstand the substantial pressure exerted during the compaction process. Moreover, its resistance to deformation and cracking under stress guarantees a long service life for the granulator, ultimately leading to reduced maintenance requirements and operational downtime.
Thus, the utilization of Q235 boiler steel in the construction of the extrusion granulator not only ensures the robustness and longevity of the machinery but also underpinning the reliability and consistency of the granulation process.
The double roller press granulator is a versatile tool for dry powder granulation, comfortably processing a wide array of chemical and organic materials.
1. Raw Materials in NPK Fertilizer Production
A double roller extrusion granulator, utilizing roller compaction technology, efficiently processes an extensive range of materials in fertilizer production. These materials include compound fertilizers such as ammonium sulfate and ammonium nitrate, phosphate fertilizers like monoammonium phosphate (MAP) and diammonium phosphate (DAP), potash, and so on.
2. Handling Organic Materials for Fertilizer Production
Besides chemical fertilizers, the granulator excels in processing organic materials pivotal for organic fertilizer production. Examples include animal manure, compost, and sludge, which are crucial components of organic fertilizers. Its efficiency, adaptability, and reliability make it a preferred choice for organic fertilizer manufacturers seeking high-quality granulation proposals.
3. Other Applications in Dry Powder Granulation
Beyond fertilizer production, the double roller extrusion granulator finds application in various industries requiring dry powder granulation. Additionally, it’s utilized in the chemical industry for the compaction of powdered materials into solid forms, facilitating handling and storage. Moreover, the granulator efficiently handles mineral powders, contributing to applications such as metallurgy and mining. For instance, it processes mineral powders into dense granules for use in metallurgical processes or as additives in various industrial applications.
Conclusion
With its capability to process a diverse array of materials, ranging from chemical fertilizers and organic substances to mineral powders, the double roller extrusion granulator emerges as a versatile and indispensable tool in dry powder granulation across multiple industries. Meanwhile, you should know the key for successful granulation is to understand the material’s characteristics, including particle size, moisture content, and cohesiveness. Slightly adjusting the roller gap and pressure settings allows for the production of granules with the desired density and size.
At the beginning, you must understand that maintaining a double roller extrusion granulator is essential for it to function optimally. Regular maintenance not only extends the machine’s lifespan but also ensures you get the best performance. As an operator, remember that your attention to maintenance details will prevent unexpected breakdowns and costly repairs.
1. Daily Maintenance Routine
Every day, you should start by cleaning the machine to remove any residual material that could harden and cause blockages. Furthermore, you should check the machine’s parts, such as bolts and bearings, to ensure they are tight and in good condition. Also, lubricate the moving parts to reduce wear and tear. Importantly, you should inspect the rollers and die for any signs of damage or wear. If you notice any issues, address them immediately to prevent further complications.
2. Weekly Maintenance Tasks
In addition to daily maintenance, there are tasks you should perform weekly. These include a thorough inspection of the electrical system to ensure there are no loose connections or damaged wires. Besides, you need to check the pressure of the rollers and adjust if necessary to ensure uniform granules. Furthermore, you should find professional engineers to assess the machine’s overall performance and efficiency. If you detect any irregularities, it’s crucial to troubleshoot them promptly.
3. Monthly Maintenance Checks
On a monthly basis, you should conduct more in-depth maintenance. This involves checking the gearbox oil level and quality, and replacing it if needed. Additionally, tou can examine the belts for any signs of wear or slackness and adjust or replace them accordingly. Also, you should test the machine’s safety features to ensure they are functioning correctly. Remember, safety checks are not just about compliance, but they also protect you and your workers from potential hazards.
4. Long-term Maintenance Schedule
Finally, for long-term maintenance, you should schedule downtime for the machine at least once a year. During this period, you can perform comprehensive maintenance tasks such as replacing worn-out parts, updating any outdated components, and thoroughly cleaning and inspecting every part of the machine. Additionally, you can contact us for replacement of wearing parts.
Overall, maintaining your double roller extrusion granulator requires diligence and consistency. By following the daily, weekly, monthly, and long-term maintenance schedules, you ensure the machine operates at peak performance for more than 10 years. If you have any further questions or concerns, don’t hesitate to consult the manufacturer’s manual we provide or contact our professional technician for assistance.
1. What Is The Basic Principle?
The fertilizer roller granulator machine operates on the principle of compaction and granulation. Moreover, through the application of pressure, raw materials are compacted into dense masses, which are then broken down into uniform granules. Besides, this process occurs without the use of additional moisture, making it ideal for producing dry fertilizer granules.
2. How Does The Extrusion Process Occur?
During operation, the granulator press roller machine utilizes counter-rotating rollers to exert pressure on the raw materials. Then, this pressure forces the materials to pass through the narrow gap between the rollers, resulting in compaction. As the compacted material exits the rollers, it undergoes further processing to form granules of the desired size and shape.
3. What Are The Key Components?
Key components of the roller granulating machine include the extruder, which places the counter-rotating rollers, and the feeding system, responsible for delivering raw materials to the extrusion zone. Additionally, the granulation chamber and discharge system play crucial roles in shaping and collecting the formed granules.
4. What Are the Advantages of Dry Granulation?
Dry granulation offers several advantages over traditional wet granulation methods. By eliminating the need for additional moisture, it reduces production costs and energy consumption. Moreover, dry granulation minimizes the risk of material degradation and contamination, resulting in higher-quality granules.
5. What Are Applications of Press Roller Machine?
Dry roller press granulators find application in various industries, including fertilizer production, chemical manufacturing, mining processing, and food processing. In addition, they are particularly suitable for producing granular products with specific size and density requirements, making them indispensable in modern manufacturing processes.
1. What Makes the Double Roller Extrusion Granulator Essential?
Firstly, double roller extrusion granulator serves as key equipment in compound fertilizer granulation. With advanced technology, compact structure, and low energy consumption, this device operates on the extrusion principle to swiftly form fertilizer granules ranging from 3 to 10mm in diameter.
2. Where Does the Roller Press Granulator Find Application?
Secondly, this dry granulator is indispensable in the production of special compound fertilizers of varying concentrations for diverse crops. Whether high, medium, or low concentration compounds, the roller press granulator can achieve all the results. Meanwhile, it doesn’t need drying and cooling process, which makes it suit various materials’ granulation.
3. What Are Commercial Proposals of Double Roller Press Granulator?
From an investment and economic perspective, the pellet extruder machine proves highly advantageous across several industries. For one thing, it can be applictions in fertilizer processing, feed production, and chemical industry granulation. Furthermore, it finds applications in powder material production and processing, with notable relevance in sectors such as rare earth, metallurgy, coal, biological preparations, and environmental protection engineering for sludge treatment.
4. How to Optimize Granular Fertilizer Production Efficiency?
Fourthly, to cater to customer demands effectively, our factory offers the flexibility to design and manufacture accompanying equipment. From mixers and crushers to bucket elevators and conveyors, you have many options for your fertilizer production efficiency enhancement. Additionally, automatic batching machines and rotary screening machines enhance the efficiency of compound fertilizer production lines, facilitating continuous and mechanized operations.
5. What Materials Can Be Used in the Roller Extrusion Granulator?
The double roller type fertilizers granule machine accommodates a wide array of materials for extrusion granulation. These include ammonium nitrate, urea, ammonium chloride, calcium nitrate, potassium chloride, potassium sulfate, and more. With its versatility and efficiency, this equipment seamlessly integrates into various production processes, ensuring consistent and high-quality granule formation.
In fact, water content of raw materials is a key parameter for the double roller granulator that significantly impacts the overall efficiency and quality of the granulation process. When you use our double roller type fertilizers granule machine, we recommend to maintain the materials’ moisture content of 5%-10% to achieve optimal granulating results.
Why to Control 5%-10% Material Water Content for Dry Granulation Roller Compaction?
Why is controlling the moisture important when using YSX double roller granulator? Hence, several reasons account for the significance of this specific range of water content.
- Firstly, you can ensure the proper granular forming during the press granulation process by maintaining the right moisture level in the raw materials.
- If there’s too much water (more than 10%), you may end up with wet finished granules that stick together, forming lumps. Then, it causes difficult separation and impairs the uniformity of your final products.
- Conversely, raw materials without enough moisture (less than 5%) might not support conditions of particle adhesion, leading to granules that are too dry and break down easily.
As a result, only the moisture content within the recommended range, the particles can adhere together smoothly, resulting in well-formed and sturdy granules. This ensures that the granules are resistant to breakage and can withstand handling and transportation without losing their integrity.
To conclude, finding the right moisture balance is paramount for producing high-quality granules in a double roller granulator. If you aren’t sure about the moisture content of your raw materials, feel free to send them to us. We would be more than happy to carry out an analysis for you and guide you towards the most effective process possible.
Customers often ask about the longevity and durability of our granulation machinery. Moreover, two common question are, “What is the wearing part?” or “How long does it take to replace the mold?”
What is the wearing part?
Firstly, let’s understand what worn parts refer to. In Shunxin’s roller granulator, the worn parts are the roller sheets. For one thing, two rollers are made of special alloy materials to endure high pressure and wear during the dry granulation process. For another thing, you don’t need to worry about the replacement of two rollers. If you normally use and maintain double rollers pressing granulator according to the operating instructions, the service life of 2 rollers can reach at least 6 months. However, when you find that the roller is worn or the granulation quality is getting worse, you should consider replacing it with a fresh roller.
How long does it take to replace the mold?
Secondly, you should know the time for replacing the mold. Overall, in most cases, you may need to replace the rollers within 6 months to 1 year. Furthermore, many elements will impact the particular time, including frequency of usage, raw materials’ kind and quality, and so on. To guarantee the performance of the rollers and the efficient operation of this granulator, we recommend that you regularly inspect and perform necessary maintenance. If you see that the roller is worn out or that the granulation effect is poor, it is time to replace it.
Conclusion
Our roller pressing granulator is a reliable equipment. By regularly replacing two rollers and maintaining these molds, you can keep the machine running smoothly and achieve high-quality granulation effects. All in all, we are committed to providing cost-effective organic fertilizer production proposals. Thus, choosing Shunxin’s roller granulating machine would be a wise choice. If you have any further questions or requests, we are always willing to provide assistance and support.
Maintaining your double roller extrusion granulator is essential to ensure its longevity and optimal performance. Regular upkeep not only prevents unexpected breakdowns but also guarantees that your fertilizer production runs smoothly and efficiently. Here’s a comprehensive guide on how to maintain your granulator:
Step 1: Regular Cleaning and Inspection
Firstly, to maintain your double roller press granulator effectively, it is crucial to conduct regular cleaning and inspection. At the beginning, you can start by disconnecting the power source and removing any remaining materials. Moreover, you should use a brush or compressed air to clean the rollers and the surrounding areas. Meanwhile, you can inspect the rollers for any signs of wear or damage. By keeping the machine clean and performing regular inspections, you can prevent potential issues and ensure smooth operation.
Step 2: Lubrication of Moving Parts
Secondly, proper lubrication of moving parts is essential for the efficient operation of the roller extrusion granulator. So, you may use the recommended lubricants and follow the our professional equipment manufacturer’s guidelines for lubrication intervals. Also, you can apply the lubricant to the designated points, including bearings, gears, and other moving components. Importantly, it will reduce friction, minimize wear and tear of well-lubricated parts, and extend the lifespan of the machine. Furthermore, you can regularly check the lubrication status and replenish as needed to maintain optimal performance.
Step 3: Adjustment of Roller Gap
Thirdly, the adjustment of the roller gap is a critical maintenance task for a roller compaction granulator. Because, proper roller gap settings ensure the desired granule size and density. Moreover, you should follow our recommendations for adjusting the roller gap based on the type of raw materials being processed. In addition, you should regularly check and adjust the roller gap as needed to maintain consistent granulation performance. By ensuring the correct roller gap settings, you can produce high-quality granules and prevent issues such as uneven granule size or blockages.
Step 4: Replacement of worn parts
Fourthly, parts of your granulator will inevitably wear out due to regular use. So, you must keep a close eye on components that tend to wear out quickly, such as rollers, bearings, and seals. Besides, you can inspect these parts frequently for any wear signs, including cracks, dents, or excessive wear. Once you notice that parts are worn, replace them immediately with genuine parts. Additionally, you can contact us to have new parts shipped for free shipping during the warranty period. Thus, timely replacement of worn components helps you avoid operational interruptions, maintain granulation quality, and extend the overall life of your machine.
Step 5: Optimizing Material Handling
Finally, proper material handling is key to the maintenance of a dry extrusion granulator. For example, you need to ensure that the raw materials fed into the machine meet the specified requirements in terms of moisture content, particle size, and composition. Also, you should also avoid overloading the machine to prevent undue stress and damage. Additionally, you can regularly clean the material feeding system to prevent clogs and ensure smooth material flow. By optimizing material handling practices, you can maximize the efficiency and productivity of the granulation process while minimizing wear on the machine.
Conclusion
Overall, maintaining a double roller extrusion granulator involves a combination of regular cleaning, lubrication, adjustments, part replacements, and material handling optimization. By following these maintenance guidelines diligently, you can ensure the longevity, efficiency, and quality performance of your granulation equipment. Because it not only increases productivity but also minimizes downtime and repair costs in the long run.
Here at Yushunxin, we take pride in the efficiency and performance of our double roller extrusion granulator. Besides, our engineers design this machine expertly to convert various raw materials into granules, commonly in industries like fertilizer, feed, and chemical. Moreover, one of the standout features of our granulator is that it produces granules with consistent size and hardness.
Typically, the final granule size you can expect by using our roller press granulator is in the range of 3-10mm. In other words, you can adjust the machine’s parameters to control the sizes, including the pressure and the distance between two rollers. Besides, you understand that granule size matters when it comes to applications like fertilizer production, as it affects nutrient distribution and absorption in the soil. Therefore, we ensure our granulator produce a size range optimal for you needs.
In addition to size, the hardness of the granules by dry roller press granulator is usually around 15-20N/mm2. Thus, this level of hardness ensures the granules are durable and not prone to breaking or crumbling during handling or application. As a result, it depends on the pressure by the two rollers and the composition of the raw materials.
It’s essential to note, however, that granule size and hardness can somewhat vary with different materials and granulator settings. Therefore, operators need to carefully control these parameters to achieve the desired granule characteristics.